Microencapsulation by chemical methods
Microencapsulation by chemical methods is largely developed in the industries, with productions up to several thousand tons per year. However, the technology suffers of the image of non-green technologies. The objective of this contribution is to compare the traditional approach of interfacial polymerization with interfacial cross-linking to form microcapsules, showing some advantages of the second method for applications where the encapsulated active are fragile and green technologies are required.
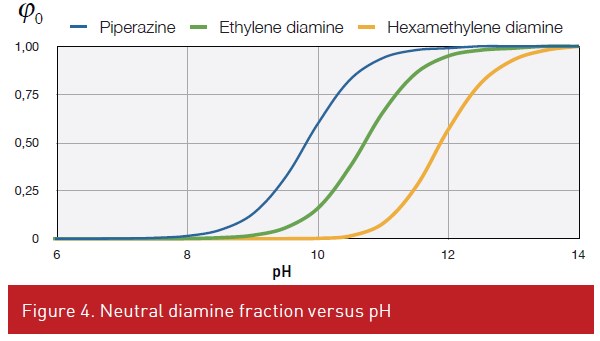
Interfacial polymerization
In the interfacial polymerization technique the wall is formed from monomers that are dissolved in the two separate phases (oil and water phase) and they polymerize at the interface of the emulsion droplets. For example, monomers such as diamine can be dissolved in the water and the aqueous phase is dispersed in the oil phase. The second monomer that is oil-soluble, for example diacid chloride, is then added and reacts with the first monomer at the interface forming the wall material. Different types of polymers may be produced by selecting different monomers but most publications refer to polyamide membrane (Figure 1).
The polyamide membrane grows in the organic phase
Morgan et al. (1959) demonstrated that the polyamide membrane grows in the organic phase. Initially, the reaction is very fast leading to dense membrane at the interface. Then the diamine has to transfer through this first layer. While not totally understood, the membrane grows while forming pores. The usual explanation is that some water are also transfer through the membrane, coalesce leading to water droplet in the membrane (Janssen and Nijenhuis, 1992). Figure 2 shows usual structure of the polyamide membrane. Figure 3 shows a diagram representing the membrane formation kinetics diffusion of the diamine from the aqueous phase to organic phase. Diamines (DA) exists in different acidform.
Only the neutral diamine fraction could be transferred in the organic phase. Neutral diamine fraction is strongly pH dependent (Figure 4). Lower pKa results in higher neutral diamine fraction at lower pH (Fig 4). An equilibrium exists between the concentrations of the neutral diamine in the organic and aqueous phase, represented by the partition constant.
Solvents are important parameters in the interfacial polymerization
Where the index o and a refers respectively to concentration in the organic and aqueous phase at the interface. Figure 5 shows the impact of the number of carbons on the partition constant and the neutral linear diamine fraction. Solvents are important parameters in the interfacial polymerization. More polar solvents gives high values of the partition constant of the hexamethylene diamine(Table 1) but are generally also more toxic (especially chloroform). Assuming that the reaction between the diamine and the diacid chloride (DC) is very fast in regard to the diffusion of the diamine, the process kinetics is given by.
where D is the diffusion coefficient in the membrane, the membrane thickness and CDA the total concentration of diamine in the aqueous phase.
While analysing last equation, one may conclude that a fast membrane formation requires a high pH (Figure 4) for high neutral diamine fraction and to select a polar solvent promoting the diamine transfer to the organic phase.
Regarding the diacid chloride, aromatic one are more reactive than linear one
The selection of a diamine is a compromise between low pKa value, generally short carbon chain and high partition constant, i.e. long carbon chain (Figure 5). Often the hexamethylene diamine is selected as an optimum. Regarding the diacid chloride, aromatic one are more reactive than linear one. However, linear diacid chlorides give more flexibility to the membrane.
One drawback of the polyamide production is the release of hydrochloric acid (HCl). This may drop the pH, especially if the aqueous phase is the dispersed phase (then lower volume). While working at high pH, this effect is not very sensible but while using low pKa diamine and then low pH, one has to verify that the buffer capacity is high enough to avoid pH drop.
Moreover, the local pH at the reaction site may be anyway lower than expected, reducing the reactivity of the diamine. In conclusion, although microcapsules made by interfacial polymerization have interesting properties, the production conditions are quite drastic (e.g. high pH) and lead to the use of toxic solvents (e.g. cyclohexane).
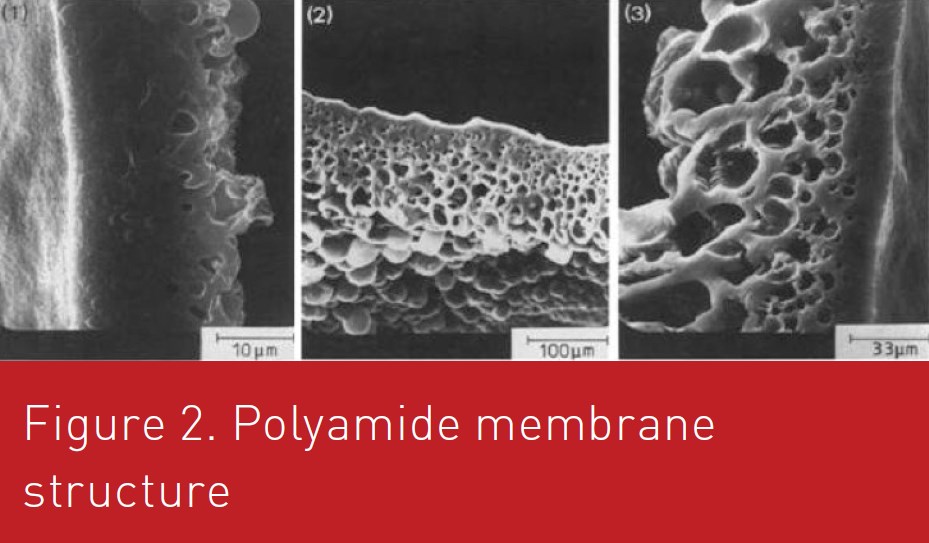
Interfacial crosslinking
While contacting an aqueous phase containing a polymer with an organic phase containing a cross-linker, a membrane is formed. If the contact is done through an emulsion, it results in microcapsules with an aqueous or organic core depending which phase is dispersed in the continuous phase. This technology is still not largely spread in industry.
These microcapsules have been essentially developed for cosmetic applications
The main development was linked to the French company, Coletica (today part of BASF) based on the work done by the group of Mrs Lévy (see page 22).These microcapsules have been essentially developed for cosmetic applications. Different polymers have been used to form such capsules but may be divided mainly in three categories: proteins, polysaccharides and polyamines. All these polymers are insoluble in the organic phase and then the membrane is formed in the aqueous phase (Figure 6).
The most usual cross-linkers are diacid chloride and diisocyanate which are only slightly soluble in water. The reaction is then quite slower then in the case of the interfacial polymerization. However, as we start from pre-polymer, limited number of cross-linking reactions is sufficient to get a membrane.
The formation of membrane is then easier with a protein than with polysaccharide
As amine functions are largely more reactive than alcohol functions, especially at medium alkaline pH (~9), the formation of membrane is then easier with a protein than with polysaccharide. Selecting polyamines (such as poly-imines or chitosan (a natural polyglucosamine ) with low pKa allows to work even at neutral or even slightly acid pH (Poncelet et al., 1991). Generally, the dissolution of the crosslinker requires a slightly polar solvent.
However, diamine has not to be transferred to organic phase, and low polarity may even favour the transfer of the cross-linker in the aqueous phase The cross-linking of the polymer leads to a gel more than a dense membrane. Under wet conditions, the membrane is quite permeable. However, when drying oil core capsules, the membrane get dense and quite impermeable (Figure 7).
Most cross-linker could react with water
Most cross-linker could react with water. It is then a competition between the polymer function and water. At the beginning the membrane is thin and cross-linker has to travel a short distance to reach amine polymer function. The membrane grows very fast. However, as the membrane thickness increases, the probability that the cross-linker react with water before to reach some free polymer function increases. High reactive crosslinker such as diacid chloride react too quickly with water leading to thin membrane while less reactive crosslinker such as di-isocyanate could migrate further from the interface to react with polymer function leading to thicker membrane (Ongmayeb, 2008). Membrane formation is slower (30 min) than through fast interfacial polymerization (a few minutes).
In conclusion, the interfacial polymer cross-linking allows forming microcapsules in mainly neutral pH, using low polar solvent (oil) and we are actually testing some cross-linker that may be considered as food grade. This technology has been successfully used for encapsulation of biocatalysts such enzymes or probiotics.
Polymerization is a technology that is largely spread in the industries
Interfacial cross-linking allows to produce capsules in softer conditions using green conditions. The encapsulation of fragile active molecules is then possible. Such capsules are biodegradable. The technology is more suitable for domains like cosmetics, food and feed and even medicine. The objective of this article was to show that the polymerization is a technology that is largely spread in the industries (e.g. textile, agrochemical …).
But this reaction has some disadvantages (e.g. toxicity of solvents) and therefore does not always encapsulate sensitive actives (e.g. enzymes). Microcapsules obtained by interfacial crosslinking is an alternative which would form microcapsules in softer conditions, using green materials (e.g. proteins, chitosan),which can be used in others applications (e.g. cosmetics, food).
Poncelet*, C. Perignon*# and G. Ongmayeb#
*Oniris and #Capsulae, Nantes France
Contact-us
"*" indicates required fields