
INNOV’IA and its subsidiaries have developed robust technological know-hows, based on multi-technologies capabilities, for producing high-performance and easy-to-use ingredients.
The technological processes allow to manufacture innovative ingredients as formulation engineered solutions, with a guaranteed industrial scalability.
INNOV’IA and subsidiaries produce on 5 plants, located in France.
The manufacturing tools have several sizes (from pilot workshops to industrial plants) and they are managed with separate production lines preventing cross contamination, and a safe & clean-in place system.
INNOV’IA and subsidiaires’ plants have a sustainable policy.
BENEFITS OF OUR TECHNOLOGIES
INNOV’IA expertises allow to assess the customers’ constraints and provide the best technological solutions in terms of particle size, density, flowability of your products.
Since early stage of the customers’ project, INNOV’IA analyses, through the proven processes of the Technomix toolbox, the various technical constraints expressed or identified in order to ensure a trusteed industrial transposition.
Then, INNOV’IA proceeds to micro-production on semi-industrial equipments to settle the constraints linked to the process (process time, cleaning of installations) and to ensure a reliable transposition on a larger scale.
INNOV’IA provides production equipments with various sizes, serving the customer design processes and producing, allowing:
- The liquid preparation of the ingredients (mixing, homogenization, temperature control cold or hot).
- The production of pre-series.
- The manufacture of your products from a few hundred kg up to several tons per day.

INNOV’IA VALUE PROPOSITION
INNOV’IA and its subsidiaries are manufacturing tailor-made ingredients by assembling multi-technologies (drying, over drying, granulation, microencapsulation (coating, spray cooling, co drying, etc) for creating unique products.
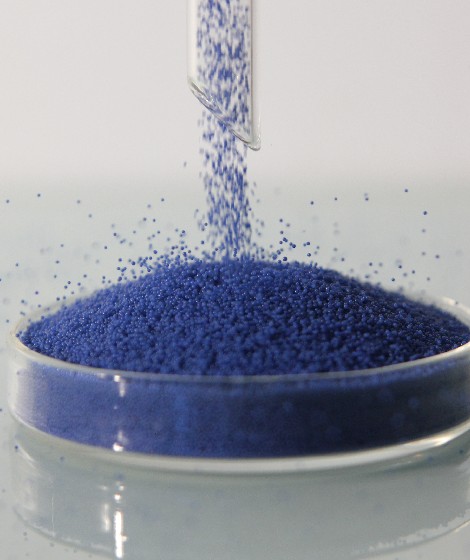