Introduction to microencapsulation
Microencapsulation encompasses various technologies that create individualized microparticles composed of a coating material and an active substance, typically ranging in size from 1 μm to 1 mm. Used in several industrial sectors, this technique offers advantages such as the protection of active ingredients, improved presentation, and precise control over their release.
Technological cost-benefit analysis
Microencapsulation offers numerous advantages but also some disadvantages that are important to consider. Here is an overview of the main points to take into account:
Advantages
- Protection of active ingredients against environmental degradation.
- Precise control over the release of active substances.
- Masking of undesirable tastes or odors.
- Improved handling of molecules.
- Possibility of targeted and prolonged release.
- Various applications in numerous industrial fields.
Disadvantages
- Potential risks to human health due to the microscopic size of the capsules.
- Use of toxic solvents in the manufacturing process.
- Difficulties in aligning with sustainable development practices.
- High production costs due to the required modern techniques.
- Durability issues in textiles (loss of more than 50% of microcapsules after 15 washes).
- Need for further research on potential risks.
Innov’ia’s expertise in microencapsulation
Innov’ia excels in microencapsulation thanks to its expertise and cutting-edge technologies, notably spray drying, which produces fine powders (50–100 μm) or microgranules (100–350 μm) while preserving the properties of active ingredients. This process is a competitive alternative to lyophilization.
Innov’ia has four spray drying towers in La Rochelle, allowing for the drying of various volumes and types of products. Its expertise also extends to co-drying and microencapsulation, addressing various industrial challenges. In the pharmaceutical sector, Innov’ia is FSSC22000 certified for human food and FAMI-QS certified for animal feed, ensuring high production quality.
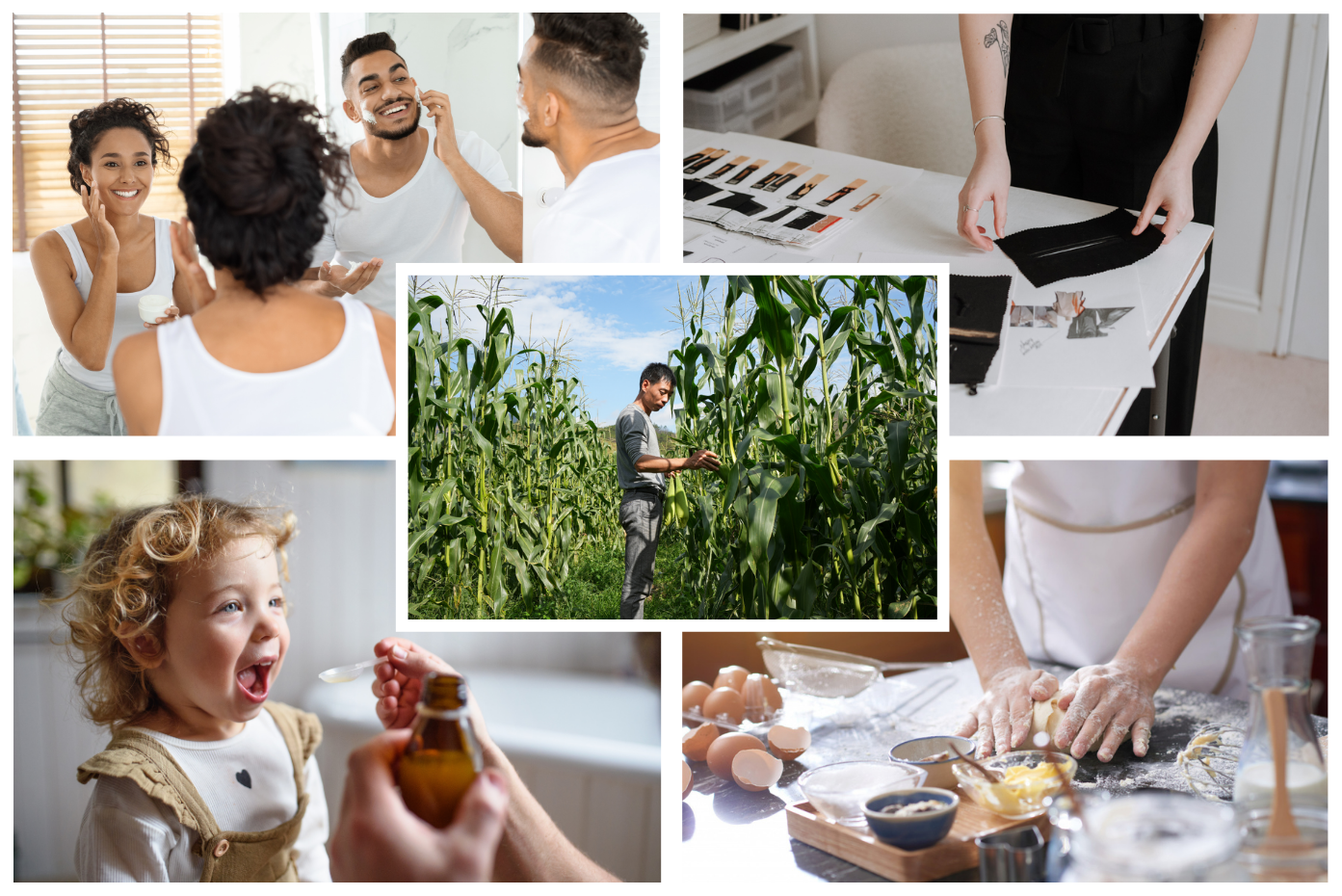
Advanced agri-food applications
Microencapsulation is widely used in the food industry to protect, stabilize, and control the release of active ingredients. It improves the quality, shelf life, and functional properties of foods.
Encapsulation of polyunsaturated fatty acids and fat-soluble vitamins
A major application concerns the encapsulation of polyunsaturated fatty acids and fat-soluble vitamins (A, D, and E) to protect them against oxidation and degradation. For example, encapsulating vitamin D₂ in casein micelles has demonstrated effective protection against UV-induced degradation. This approach preserves the nutritional properties of fortified foods while increasing their shelf life.
Masking undesirable flavors and odors
Microencapsulation is also used to mask undesirable flavors and odors of certain functional ingredients. This technique allows incorporating health-beneficial compounds into foods without altering their organoleptic properties. Additionally, encapsulation can be employed to control the release of aromas, notably in chewing gums, offering a prolonged gustatory experience.
Commonly used encapsulation techniques
The most commonly used encapsulation techniques in the food industry include spray drying, spray cooling (or prilling), extrusion coating, fluidized bed coating, liposome entrapment, and coacervation. Each method offers specific advantages depending on the ingredient to be encapsulated and the intended application. For example, liposome entrapment is particularly suited for the manufacture of cheeses, food emulsions like spreads, margarine, or mayonnaise.
Controlled release of encapsulated agents
The controlled release of encapsulated agents can be triggered by various stimuli, such as contact with saliva, changes in pH, temperature, irradiation, or osmotic shock. This property allows designing functional foods with targeted release, thus optimizing the effectiveness and bioavailability of active ingredients.
Product stability and durability
Food microencapsulation also offers advantages in terms of product stability and durability. It allows increasing the concentration of active ingredients up to 87%. Moreover, this technology enables the production of dietary supplements from products that were previously unusable due to side effects, such as heartburn, by protecting the active ingredient from gastric juices and delivering it directly to the intestine.
In conclusion, microencapsulation in the food industry is a constantly evolving technology, offering innovative solutions to improve the quality, functionality, and nutritional value of foods. Its growing use demonstrates its potential to meet the challenges of the modern agri-food industry, particularly in terms of nutrient preservation, controlled release, and enhancement of organoleptic properties.
Applications in the pharmaceutical industry
In the pharmaceutical industry, microencapsulation offers significant advantages for drug formulation and administration. It improves the stability of active ingredients, masks unpleasant tastes, and allows more precise control over the release of drugs in the body. Microencapsulation is used to develop prolonged or targeted release systems, thus optimizing therapeutic efficacy while reducing side effects. For example, microcapsules can be designed to gradually release a drug over an extended period, improving patient compliance and reducing dosing frequency. Moreover, this technology enables the encapsulation of sensitive active ingredients, such as proteins or peptides, protecting them against enzymatic degradation and increasing their bioavailability. Microencapsulation also paves the way for new therapeutic approaches, such as the administration of encapsulated cells for the treatment of chronic diseases.
Controlled release techniques
Controlled drug release is a concept that emerged in the 1930s but experienced significant development from the 1970s onwards, notably thanks to the introduction of the “therapeutic system” concept by the company Alza. This approach aims to control not only the rate but also the site of active ingredient release, thus offering numerous therapeutic advantages. Controlled release techniques include various systems such as prolonged, delayed, pulsed, or programmed release, each adapted to specific needs. These systems can be designed for oral, transdermal, or respiratory administration, using polymeric matrices, reservoir systems, or advanced encapsulation technologies. The main objective is to achieve a zero-order release profile, independent of time and biological variables, allowing stable plasma concentrations to be maintained, reducing dosing frequency, and improving treatment compliance while minimizing side effects.
Coating materials: natural vs. synthetic polymers
Coating materials used in microencapsulation can be classified into two main categories: natural polymers and synthetic polymers. Natural polymers, such as starch, proteins, and polysaccharides, offer advantages in terms of biocompatibility and biodegradability. They are often preferred for pharmaceutical and food applications due to their low toxicity. In contrast, synthetic polymers like polyethylene, PVC, and polyacrylates offer greater versatility in terms of physicochemical properties and release control. They allow better control over particle size and the release kinetics of the active ingredient. However, their environmental impact is generally more significant, and some may present risks of residual toxicity. The choice between natural and synthetic polymers depends on the specific application, regulatory requirements, and considerations of naturalness.
Pricing and target clientele
Microencapsulation is an advanced technology that finds applications in many industrial sectors, but its cost and complexity make it a solution primarily suited to companies with specific needs and the necessary resources to implement it. Here is an overview of the main users and cost considerations:
Main users
- Pharmaceutical industry: Pharmaceutical laboratories widely use microencapsulation to improve the efficacy and stability of drugs, as well as to develop controlled release systems.
- Food industry: Food manufacturers employ this technology to protect sensitive ingredients, mask undesirable tastes, or improve product shelf life.
- Cosmetic industry: Cosmetic companies use microencapsulation to stabilize active ingredients and enhance their release in care products.
- Agrochemical industry: Pesticide and fertilizer manufacturers use this technique to improve efficacy and reduce the environmental impact of their products.
Textile industry: Smart textile manufacturers integrate microcapsules to create specific properties such as thermoregulation or fragrance release.
Cost considerations
The cost of microencapsulation can vary considerably depending on several factors:
- Process complexity: More advanced techniques like complex coacervation or prilling are generally more expensive than simpler methods like spray drying.
- Nature of materials: The use of specialized synthetic polymers or rare biopolymers can significantly increase costs.
- Production scale: Unit costs tend to decrease with increased production volumes, but the initial investment in equipment can be high.
- Regulatory requirements: In the pharmaceutical and food industries, costs related to regulatory compliance (e.g., GMP certifications) can be substantial.
- Research and development: Developing specific formulations may require significant R&D investments.
Although it is difficult to provide precise figures without knowing the specifics of each project, the cost of microencapsulation can range from a few euros to several hundred euros per kilogram of final product, depending on complexity and production scale. For companies considering using this technology, it is recommended to conduct a detailed cost-benefit analysis, taking into account not only direct production costs but also potential advantages in terms of product quality improvement, market differentiation, and operational efficiency.
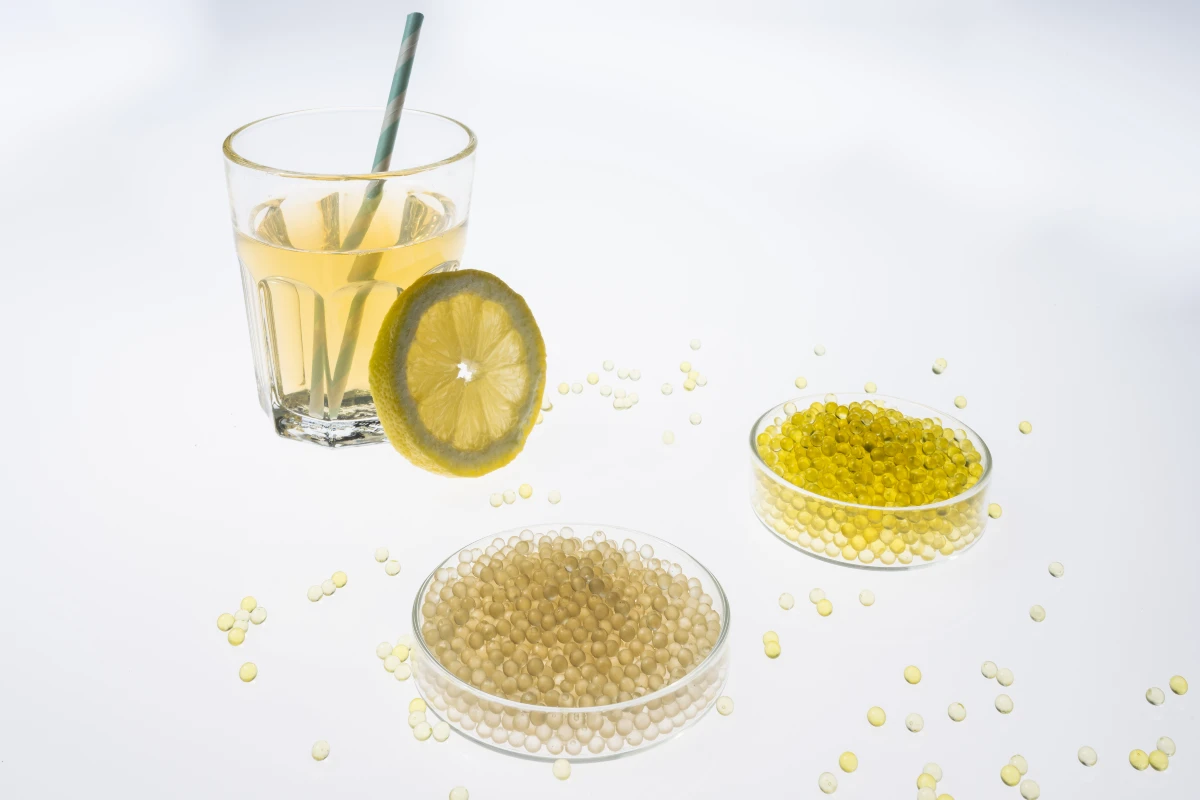
FAQ
It protects active ingredients, improves their presentation, controls their release, masks undesirable tastes or odors, and improves the handling of molecules.
Disadvantages include potential risks to human health, use of toxic solvents, difficulties in sustainable development, high production costs, and durability issues.
The pharmaceutical, food, cosmetic, agrochemical, textile industries, and many others.
Innov’ia uses processes like spray drying and prilling to produce fine powders or microgranules, preserving the properties of active ingredients and meeting clients’ specific needs.
Costs vary depending on the complexity of the process, materials, production scale, and regulatory requirements.
Microencapsulation is a technology that protects an active ingredient within a microparticle, increasing its stability and enabling controlled release.
Table of contents
Contact-us
"*" indicates required fields